What is a Master Production Schedule (MPS)?
By Mukesh Variyani April 19, 2024 Business
Planning and accuracy are crucial in the field of manufacturing and production. One of the key tools in the production planning process is the Master Production Schedule (MPS). For those wondering what is a Master Production Schedule, it’s a strategic document that outlines what a company needs to produce, the quantity, and the time frame. It acts as a crucial bridge between high-level business planning and day-to-day factory operations. Anyone involved in supply chain management, production planning, or operations can benefit greatly from understanding how the MPS functions.
The Fundamentals of the Master Production Schedule
At its core, the Master Production Schedule is a detailed timeline that identifies which products to manufacture, in what quantities, and when they should be produced. In the short term, the schedule is usually fixed, but over time it can be adjusted to respond to changes in demand, resource availability, or production capabilities. As the foundation of the production planning process, the MPS directly influences materials requirement planning (MRP), resource management, and overall manufacturing efficiency.
Key Components of a Master Production Schedule
A well-structured master production schedule consists of several critical elements that ensure clarity and execution efficiency.
Product identification
Each product listed in the MPS is clearly defined, usually with a unique ID and detailed specifications, to avoid confusion in the manufacturing phase.
Quantities
The master production schedule outlines the exact quantities of each product that need to be manufactured, aligning production with forecasted demand.
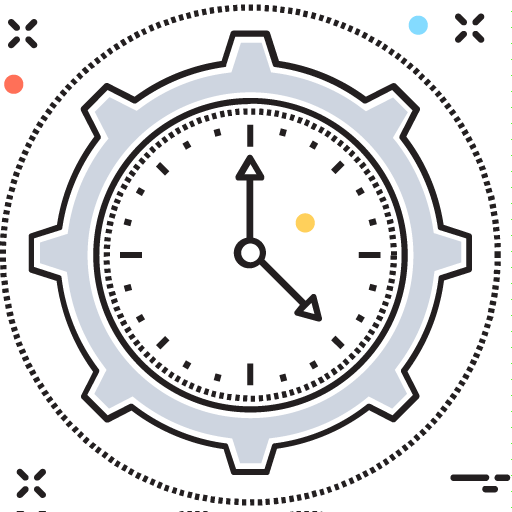
Timing
The schedule details production start and completion dates for each item, which is vital for an efficient production planning process.
Resources
Although not always directly specified in the MPS, understanding the labor, equipment, and materials needed supports the successful implementation of the master production schedule.
Challenges in the Implementation of MPS
While the Master Production Schedule is an essential part of the production planning process, implementing it effectively comes with certain challenges:
Demand Forecasting
One of the core elements of What is a Master Production Schedule involves anticipating customer needs. Inaccurate demand forecasting can disrupt the entire production planning process.
Resource Limitations
The Master Production Schedule can face disruptions when there are insufficient materials, manpower, or machine availability. Proper resource planning is vital to uphold the integrity of the production planning process.
Data integrity
Accurate and timely data is crucial for an effective Master Production Schedule. Errors in input can result in flawed outputs, affecting the overall production planning process.
Benefits of Putting an MPS in Place
Implementing the Master Production Schedule offers several strategic advantages within the production planning process:
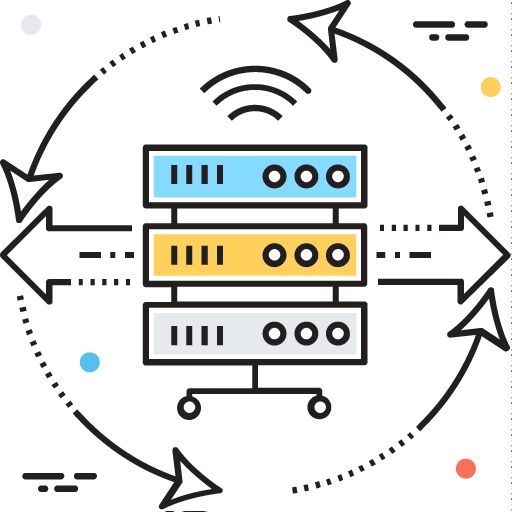
Enhanced Forecast Accuracy
With a well-structured Master Production Schedule, businesses can better align production with market demand, avoiding stockouts and excess inventory.
Effective Resource Allocation
The MPS provides visibility into what needs to be produced and when, optimizing labor, material, and machine usage in the production planning process.
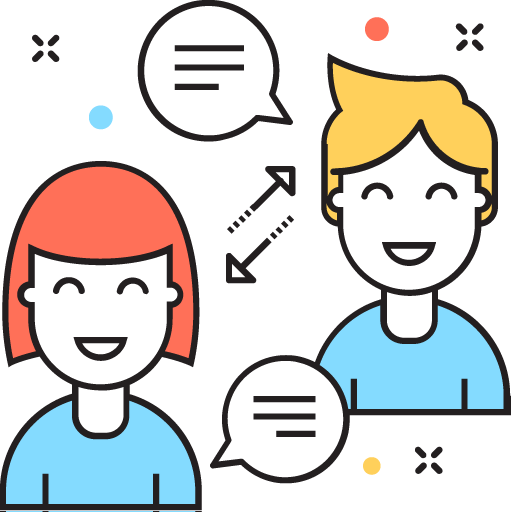
Enhanced Communication
A centralized Master Production Schedule ensures that all departments procurement, production, and sales work in coordination and have access to consistent planning data.
Enhanced Flexibility
By regularly updating the Master Production Schedule, companies can respond more flexibly to changes in demand, supplier issues, or internal production delays making the production planning process more adaptive.
Conclusion
To sum up, understanding what is a Master Production Schedule is essential for any organization engaged in the manufacturing sector. The Master Production Schedule acts as a blueprint for the production planning process, detailing what needs to be produced, in what quantity, and by when. By accurately aligning production activities with demand forecasts and resource availability, businesses can ensure consistency, regulatory compliance, and product quality. Maintaining an effective and up-to-date schedule not only improves operational efficiency but also helps safeguard customer satisfaction and trust.
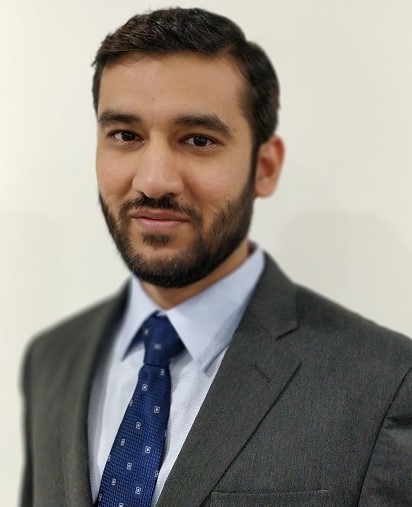
Mukesh Variyani
MD, Finbyz Tech Pvt Ltd