Chemical Engineering Software: Transforming Processes and Innovations
By Mukesh Variyani April 9, 2024 Business
.png)
Advanced technology is now indispensable in the complex field of chemical engineering, where efficiency and precision are paramount. Among the most transformative tools reshaping the industry is software, especially Chemical ERP Software, which is revolutionizing how processes are designed, analyzed, and optimized. From simulation and modelling to process control and data analytics, Chemical ERP solutions play a vital role in driving innovation and improving operational efficiency across various industries.
Understanding Chemical ERP Software
Chemical ERP Software encompasses a broad spectrum of tools tailored to the unique demands of the chemical sector. These solutions use mathematical models and computational algorithms to simulate chemical reactions, forecast outcomes, and enhance efficiency. They empower engineers with precision and speed in process definition, design, and problem-solving making them invaluable in Chemical Manufacturing ERP environments.
Modelling and Simulation
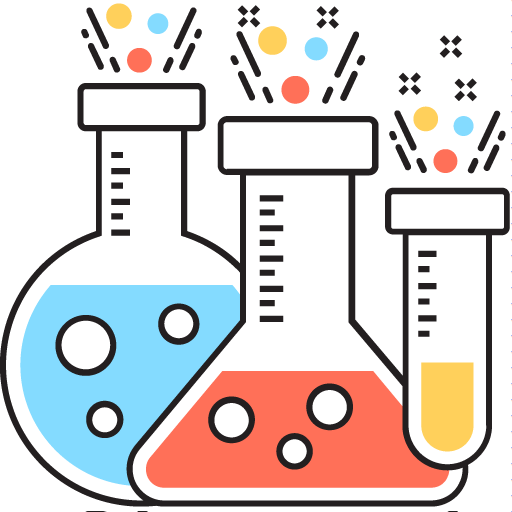
Simulation software forms the backbone of ERP for Chemical Industry, allowing engineers to create virtual models of real-world processes. By inputting data such as reaction times, chemical compositions, and operating conditions, engineers can predict system behavior across multiple scenarios. These simulations provide valuable insights that help avoid bottlenecks, refine parameters, and enhance performance.
Additionally, modelling tools within chemical ERP platforms enable engineers to develop mathematical representations of processes, facilitating optimization and predictive analysis. Technologies such as CFD and FEA allow for accurate forecasting of fluid flow, heat transfer, and mass transport within reactors and pipelines crucial for any Chemical Manufacturing ERP strategy focused on efficiency and cost-effectiveness.
Development and Improvement of Processes
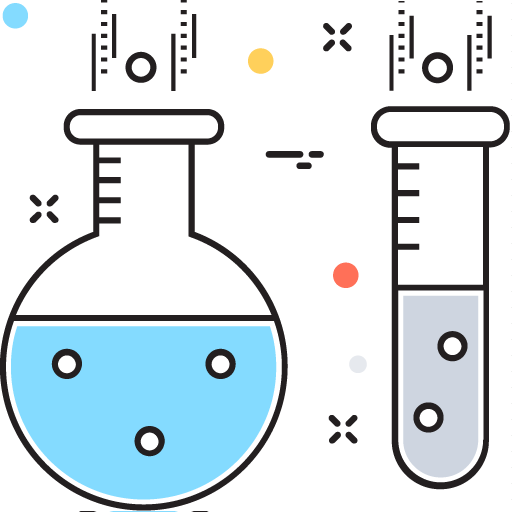
Chemical ERP Software plays a pivotal role in designing and refining industrial processes. Engineers can explore alternative configurations, evaluate equipment choices, and fine-tune conditions using simulation tools embedded in Chemical Manufacturing ERP platforms. This capability is particularly useful when designing new plants or upgrading existing ones, offering cost savings, improved safety, and higher throughput.
Furthermore, optimization modules in ERP for Chemical Industry> use techniques such as neural networks, linear programming, and genetic algorithms to fine-tune production parameters. These tools help businesses minimize energy use, improve product yield, and maintain compliance ensuring competitiveness and sustainability in the long run.
Automation and Process Control
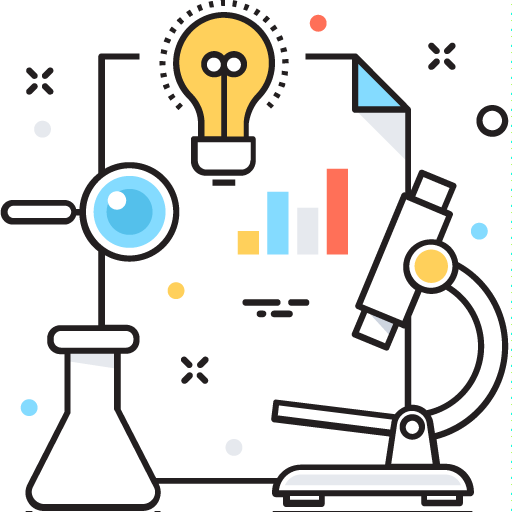
Beyond simulation and modelling, Chemical ERP Software enhances automation and real-time process control. By leveraging real-time data collection and intelligent monitoring systems, ERP tools ensure accurate control over process variables such as temperature, pressure, and flow rates vital for maintaining product quality and compliance in regulated environments.
Moreover, new paths for predictive and adaptive control have been made possible by the fusion of machine learning (ML) and artificial intelligence (AI) algorithms. These smart systems anticipate disruptions, automatically adjust settings, and ensure minimal downtime improving safety, reducing costs, and supporting sustainability goals.
Innovations and Upcoming Patterns
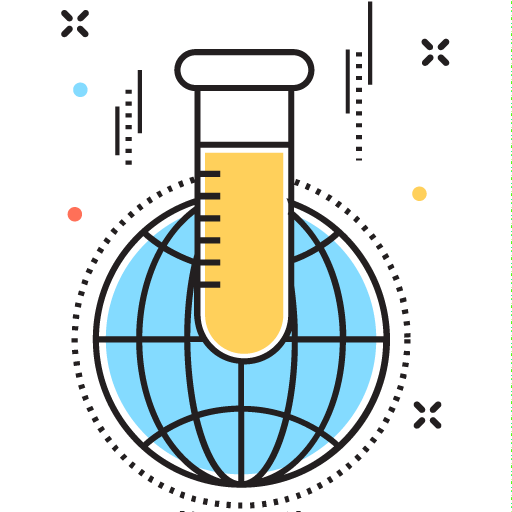
As technology continues to evolve, chemical engineering software especially ERP systems will see new dimensions of growth. Tools like digital twins, AR, and cloud-based platforms are redefining how engineers design and control processes. Digital twins, in particular, synchronize physical systems with virtual replicas for real-time performance tracking and maintenance planning adding immense value to Chemical Manufacturing ERP implementations.
The fusion of big data and IoT within Chemical ERP Software offers unmatched opportunities for real-time analytics and performance optimization. By leveraging live sensor data and operational feedback, engineers can identify inefficiencies, detect anomalies, and implement continuous improvements. These capabilities empower companies to remain agile and responsive in today’s dynamic market environment.
Conclusion
In conclusion, Chemical ERP Software has revolutionized the chemical engineering landscape, enabling engineers to drive innovation, streamline operations, and tackle complex challenges with precision. From process modelling to automation and advanced analytics, these tools are at the core of every stage in the engineering lifecycle. As the field evolves, the role of ERP for Chemical Industry will become even more critical in fostering sustainability, enhancing productivity, and maintaining competitiveness.
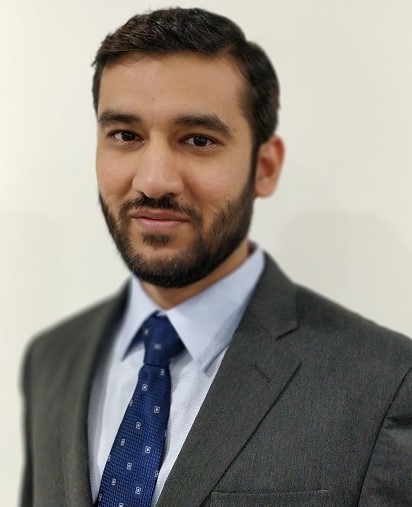
Mukesh Variyani
MD, Finbyz Tech Pvt Ltd